Fluoropolymer Exchangers
Problem
Tubing turns white after prolonged service (above solution interface).
Cause
Permeation of fluid through tubing wall and delamination of crystalline structure due to high temperature/pressure operation.
Solution
Check application/pressure rating of coil, adjust supply to not exceed coil rating or replace with higher temperature rated material.
Problem
Fluoropolymer tubing split or swelled above solution interface.
Cause
Coil operated on steam service without vacuum breaker.
Solution
Install vacuum breaker on coil supply. Repair/replace coil as required.
Cause
Coil operated at higher than rated pressure.
Solution
Check/verify steam/water source and compare to catalog rating of coil. Reduce pressure and temperature of supply. Repair or replace coil with higher pressure rated material as required or available.
Cause
Coil operated at higher than rated temperature. While pressure reducers regulate pressure in a system they do not regulate temperature that can exceed the rated values of the coil.
Solution
Verify temperature/pressures provided to coil and replace with a higher temperature rated material were required.
Problem
Fluoropolymer sheath melted, split or distorted
Cause
Heater operated with low liquid level without proper thermal protection. Check/test wiring and thermal protector to verify operation.
Solution
Repair/replace heater as required.
Cause
Heater operated at higher than rated voltage. Check/verify power supplies and compare to nameplate rating of element.
Solution
Correct voltage and replace heater as required.
Cause
Viscous or concentrated solution. Dense or concentrated solutions impede heat flow from the elements and can cause localized overheating and damage to the fluoropolymer sheath.
Solution
Increased mixing of the solution near the element can reduce the problem but replacement of the heater with a de-rated/more open design is preferable.
Cause
Buildup on the sheath. Any buildup between the formed passes on a Fluoropolymer heater will cause localized overheating and can cause melting of the sheath material.
Solution
Periodic cleaning can reduce the buildup and overheating. Open type designed, over-the-side model heaters should also be considered as replacement options. Vari-power heaters can be considered for low power requirement installations. Bottom designs with tight spacing should be avoided in any application where buildup or sedimentation is possible.
Cause
Operation in liquids that polymerize or crystallize when heated. Buildup on the fluoropolymer sheath will limit heat transfer, causing localized overheating which may melt the sheath.
Solution
These solutions can only be heated with de-rated heaters or through indirect type heating methods. Either replace heaters with open, derated design (2.5 WSI or less) or switch heating methods.
Cause
Thermal protector pulled up out of position during installation or replacement. The thermal protector only measures the sheath temperature directly adjacent to where it is mounted.
Solution
The thermal protector must be fully seated into base of the thermal well to work properly.Verify installation of thermal protector. Replace heater as required.
Cause
Thermowell tubes full of solution. Any fluid inside the Thermowell will act as a coolant and delay the switching point of the protector device until the fluid is boiled away. Care should be taken to ensure the well is not damaged, the heater junction box is sealed properly, and that the excessive moisture is prevented from entering.
Solution
Periodic inspection of the interior of the junction box and thermal well should be considered in unusually wet installations or in solutions operating over 180 degrees F. If solution is found in the Thermowell, a pressure test (5 PSI) should be performed to verify integrity.
Cause
Thermowell retainer bracket removed, out of position or damaged. Since the retainer bracket holds the thermal protector against the element at the top of the hotzone, damage to or misalignment can affect the response time and performance of the protector.
Solution
Reposition the bracket and Thermowell if heater is serviceable. Replace heater if necessary.
Cause
Localized overheating caused by operation in a confined area. If fluoropolymer heaters are operated in too small of an area that effectively limits their ability to dissipate the energy they produce, localized overheating and melting may occur.
Solution
The heater should either be moved to a more open area or solution circulation should be added to assist in heat transfer. Replace heater if necessary.
Cause
Improper forming clearance or compressed passes on the element. Formed elements should not be contacting adjacent passes under any type of pressure. While incidental element contact normally will not cause problems, compressed elements in high temperature or viscous fluids will cause excessive localized overheating and melting.
Solution
Usually element contact spots can be opened up by hand forming. If contact pressure remains the element should be returned to factory.
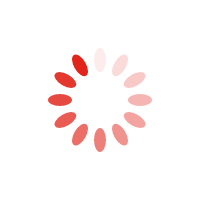